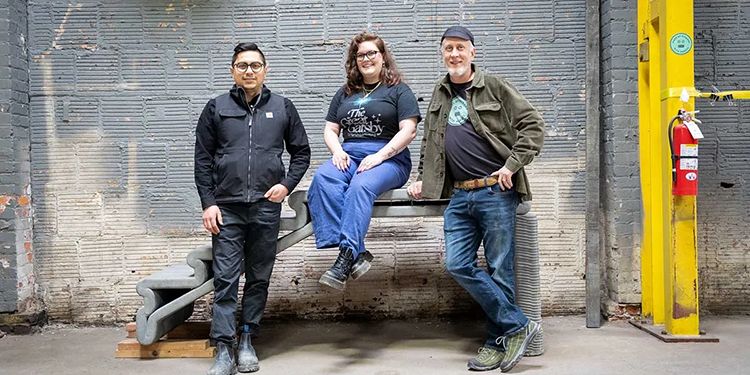
April 18, 2022
Could 3D housing be in Detroit’s future?
Christine Ferretti | Bridge Detroit
A shortage of affordable housing has Detroit exploring whether a 3D-printing robot could help.
A robotics company in southwest Detroit is hoping so and plans to deliver the city’s first factory-printed concrete home to the Islandview neighborhood later this year.
It’s billed as faster, low-cost and nonprofits, state housing and city officials say it’s a practice gaining momentum across the globe to increase move-in ready housing stock in distressed communities. The emerging technology is being explored as one tool to tackle the massive problem but the long-term sustainability and benefits aren’t yet known.
“We believe this is one way to start building better homes, more homes, faster,” said Evelyn Woodman, who co-founded Citizen Robotics in Detroit with her father, Tom Woodman.
The nonprofit launched just over two years ago and has other 3D home building projects planned for Flint and Grosse Pointe Woods. In Detroit, the company intends to build an 850-square-foot, two-bedroom, one-bath house geared toward senior living.
The project, designed by Brian Cook of Develop Architecture, president of the Detroit chapter of the National Organization of Minority Architects, is expected to get underway after the company finalizes the purchase of a Detroit Land Bank Authority parcel where it will be built.
Citizen Robotics Executive Director Tom Woodman said his company chose Detroit and Flint for its initial projects because they have vast amounts of land and demand for affordable housing.
“The situation is dire. They are striving for solutions,” he told BridgeDetroit. “In this case, it’s the disruptive technology you want: better, faster, cheaper. But it’s going to take a minute to get there.”
The single-family home planned for Detroit is anticipated to be the first state-funded 3D printed house in Michigan. It’s being financed through the Neighborhood Housing Initiatives Division of the Michigan State Housing Development Authority, said Katie Bach, a spokeswoman for MSHDA.
MSHDA is covering about $150,000 in construction costs for the partnership project between the state, a nonprofit group, the land bank and Citizen Robotics. The home, Bach said, will serve as a “proof of concept project” to help state officials determine if 3D home building is sustainable, cost-effective and energy efficient.
The house will be marketed to low-income buyers at 80% of the area median income, which is $50,240 or less for a two-person household in Detroit. The design and location are being finalized.
“MSHDA is exploring the possibility of encouraging the use of 3D technology to construct infill affordable, move-in ready homes in neighborhoods,” Bach said in an email. “This pilot project is expected to help determine the feasibility of the 3D concept as we explore creative solutions to address Michigan’s housing supply shortages.”
For Citizen Robotics, it will be the first completed home. It will be printed in sections in the company’s warehouse near Michigan Central in Corktown and transported to Islandview for assembly.
Concrete construction is air-tight, noted Woodman, who said he estimates it will reduce energy consumption by about 80% over time. Another benefit of 3D printing, he said, is that the housing design can be adapted to meet the needs of Detroit’s varying communities.
One thing that’s “broken in homebuilding,” he said, is “who gets to decide what gets built and where.
“Community engagement is not an afterthought for us,” Woodman said.
Detroit City Councilman Coleman A. Young II told BridgeDetroit he has a vision of his own for testing out the technology. It calls for 3D construction of multi-family homes in the city’s most impoverished neighborhoods.
“I need to do all I can to be able to make sure within my power that we are able to provide housing for those who need it the most,” said Young, an at-large councilman and the son of the city’s first Black mayor. “I want a pilot program to address the issues with affordable housing in areas that are the hardest hit.”
Young said his plan is in the preliminary stages but it has begun with an analysis from the council’s Legislative Policy Division. He said he’s seeking input from the city’s Housing and Revitalization Department and evaluating how a 3D printer could be acquired and the cost.
Woodman said there are a half-dozen styles of 3D printers that run from $275,000 to $1 million and he hasn’t heard of any municipalities that have purchased one thus far.
Young’s proposal comes as the city, affordable housing advocates and philanthropic partners are evaluating ways to renovate Detroit’s aging houses and bolster home repair programs and equity in mortgage lending.
Last month, Detroit Future City’s Center for Equity, Engagement and Research released a study that found lending has improved in Detroit over the past decade but many areas see few, if any, mortgage loans each year. Credit challenges, unfavorable debt-to-income ratios and bias in property appraisals are among the issues that put Black buyers even further behind.
“We have issues with diversity, equity and exclusion in terms of the issue of single-family housing and zoning. I want to open that up and make it affordable for people in the city of Detroit who are hurting the most,” said Young, adding he’d like a pilot to be targeted for “extremely low-income” residents at about 30% of the area median income – or $18,840 or less for a two-person household.
Last summer, Gov. Gretchen Whitmer joined with Detroit Mayor Mike Duggan and Citizen Robotics at the nonprofit’s warehouse to announce the state’s plan to invest $100 million in federal COVID-19 relief funding toward the construction of thousands of affordable homes statewide.
Young said it’s too early to know whether his vision will coincide with Duggan’s administration.
Julie Schneider, who heads the city’s Housing and Revitalization Department, said 3D home building is relatively new but the administration is “open to learning more.”
“The City’s policy has been investing our resources into quality housing that will stand the test of time and provide quality affordable housing for decades to come,” Schneider said in a statement “Homes printed using 3D technology may very well prove to be more durable than the materials used today, but we don’t know the full picture yet, as this is still a new technology and industry. That said, it is something that we are certainly open to learning more about and would consider if 3D-printed homes are indeed a worthy investment of housing dollars.”
‘Build what people want’
A University of Michigan study last fall estimated families in nearly 38,000 Detroit households lived in inadequate housing with major issues including exposed wires or electrical problems, broken furnaces or heating problems, or lack of hot or running water.
Woodman said the 3D technology can’t be used for repairs on the city’s existing wood-built homes – apart from a new concrete front stoop – but 3D shouldn’t be discounted because of it.
“The fact that it can’t do much toward rehabbing other old houses, I sort of say ‘so what.’ Somebody has got to focus on scattered site infill,” he said. “Nobody does it because it’s the hardest thing to do, but it’s necessary to create walkable, 15-minute neighborhoods.”
The land bank has control of the majority of the city’s vacant parcels. It has an inventory of more than 76,000 properties and most – close to 63,000 – are vacant lots.
“If we have land as an asset, it’s only an asset if you build on it,” Woodman said. “Let’s build what people want.”
Young said his intention is to start small and would begin with pinpointing equipment costs. Work also must be done, he said, to determine what material would be used, its longevity and where the houses would go, although he noted areas throughout Detroit are primed for it.
The U.S. Department of Housing and Urban Development doesn’t have an opinion on building materials so there’s been no federal guidance on the matter that Detroit officials are aware of.
“I felt this could be an opportunity if done right,” said Young, but he stressed “I’m not saying we will solve all of the city’s housing problems with this technology. It’s not going to be a panacea and silver bullet.”
‘Can we adopt it?’
In recent years, groups in Detroit have experimented with the trends of tiny homes and shipping container homes and buildings. Woodman said he doesn’t see 3D-printed housing as a fad.
“We’ve got precedent to draw on. We’re not inventing this method,” he said. “We’re tweaking it out for our purposes.”
The first full 3D printed home in the country was unveiled at Austin’s South by Southwest conference in 2018. The 650-square-foot concrete home was printed onsite, and cost approximately $10,000 to build, according to the LPD report.
Since then, a 3D project has been underway in southern Mexico to bring 50 homes to a poverty-stricken neighborhood that is prone to earthquakes and flooding.
Habitat for Humanity has partnered on several 3D-printed home projects, including one built last fall in Williamsburg, Virginia. Habitat Detroit and other Habitat affiliates are quietly conducting a similar analysis, said Stephanie Osterland, CEO of Habitat for Humanity Detroit.
“Right now, we’re heavily into the feasibility stage. What is the cost effectiveness of doing it? Do homebuyers want this type of construction? How hard is it to do and how quickly can we adopt it?,” she said. “It’s worth the time and the diligence to evaluate whether or not it can be a solution.”
Citizen Robotics initially targeted Detroit’s Woodbridge community for the 3D home pilot, but changed course due to costs associated with preparing the site owned by Woodbridge Neighborhood Development.
In recent years, Woodbridge has conducted workshops, community meetings and surveys to develop guidelines for infill housing in the 2,383-household neighborhood and to provide guidance for future developers.
Christine Holmes, the community improvement organization’s director of policy and property development, said residents are interested in single-family housing as well as preserving the historic character of the housing stock.
The 3D project, which would have constructed a small, single-story home, was welcomed by neighbors, particularly for the benefit of longtimers who might need to downsize, she said.
“This would be a way to make something that is more accessible to a senior or somebody who might have mobility problems,” said Holmes, noting the group remains open to the technology.
“A smaller footprint in general in housing is becoming more desirable,” she said. “It provides options for people. The fact that it would be 3D-printed doesn’t change that option.”
The conventional cost to build an average sized three-bedroom house is between $250,000 to $320,000. Building the same home with 3D printing technology would cost from 20% to 40% less – or between $140,000 to $240,000, the LPD analysis notes.
“The biggest roadblock, arguably, is government regulations regarding what can or cannot be allowed as a means of construction,” LPD’s report reads. “Government regulations and construction permits vary wildly across the globe. But one thing they all have in common is the reluctance of public bodies to allow cutting-edge technology to be used by the general population at such an early stage.”
Osterland said for Habitat, it’s critical to explore 3D and steel frame housing as construction costs remain high and climbed another 20% last year.
“That means for every four projects we do, that’s a whole other project we couldn’t do,” she said.
As costs go up, the more Habitat has to rely on philanthropic partners to cover gaps caused by property appraisal disparities. The demand is great for single-family homes and Habitat gets about 125 online intake forms per month from those interested in home ownership, she said.
“We’re not even close to meeting that demand. There are people in need of safe and affordable housing like no other,” Osterland said. “Detroit is accepting of innovation. Whether it catches on and if it makes sense to do at a mass scale, that’s still to be determined.”